Static Beat: How To Take a Static Survey
- Published: August 01, 2010, By By Dr. Kelly Robinson Contributing Editor
Static can cause a variety of problems in film production, coating, converting, sheeting, and packaging operations. Charged surfaces attract dust. Static causes cut sheets to stick and jam. High levels of static cause sparks that can reset machine logic, damage electronic components, ignite flammable vapors, and injure personnel.
When solving static problems, one challenge is that static comes and goes. Static problems are intermittent. Several good problem-solving methods commonly used to find the root cause begin by answering a few key questions: When did the problem start? Which products are affected and which are not? What process elements or set points might have caused the problem?
Being able to answer these questions with reliable data helps maintain a trouble-free process and enables the rapid resolution of static problems. I have used two different strategies for taking static measurements for process verification and to help diagnose problems: Static Surveys and Control Charts. Both methods establish baseline measurements for a process that is running normally. Deviations from these normal levels help identify the start of a static problem, document which products are affected, and help identify the root cause of the problem.
Let's focus on how to do a Static Survey. The survey for a simple rewind process is shown in Figure 1, in which the material flow through the operation has been divided into three groups: Incoming Materials, Process, and Outgoing Materials. Use a handheld electrostatic fieldmeter to take measurements from the beginning of the operation through the process to the end — on the incoming rolls as they arrive, on the unwinding roll at the beginning of the line, on as many film spans midway between rollers as is feasible, on the winding roll at the end of the process, and on the finished rolls just before they are transported to your customer or to the next operation.
Begin with measurements on “Incoming Materials.” Measure rolls as delivered prior to loading them on the unwinder. If static charge is wound into an incoming roll from a prior operation, charged dust and naturally occurring ions in the air will be attracted to the outer lap of the roll. So, it is important to peel the outer lap from the roll prior to taking a measurement with your fieldmeter.
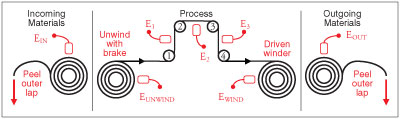
Record the data and establish what level of static is normal for incoming rolls. It is important to flag rolls that have a high level of static because the static in these “hot rolls” comes from the prior process rather than from your operation.
Next are the “Process” static measurements. For our Static Survey, use a fieldmeter to take a reading on the unwinding roll (EUNWIND), on the winding roll (EWIND), and on the three film spans midway between rollers (E1, E2, and E3).
Document the measurement locations so you can take the static readings the same way each time you do a survey. Record the readings and establish the normal levels of static in your process.
If a reading is unusually high, you can take corrective action before material leaves your operation. For example, if all other readings are normal and E1 is high, check roller 1. The roller may need to be cleaned to remove contamination; a bearing may be failing and needs to be replaced; or perhaps the roller alignment is off and needs to be corrected. In any case, the readings from your Static Survey focus attention on a specific element in which the root cause can be found and corrected.
Finally, measure your “Outgoing Materials.” The measurement technique is just like measuring “Incoming Materials.” Checking your product verifies that your customer will receive material with a normal and acceptably low level of static.
A static survey normally is scheduled to qualify a process for operation after a shutdown for maintenance or for an equipment upgrade. A static survey often is completed periodically to verify that the process is running normally. Auditing incoming materials and outgoing materials can be included as part of your normal quality control processes.
Static control expert Dr. Kelly Robinson, president of Electrostatic Answers, has 27+ years of experience in problem-solving and consulting. Contact him at 585-425-8158; kelly.robinson@electrostaticanswers.com; www.electrostaticanswers.com.