Roll Finishing-Cut & Sand
- Published: May 01, 2011, By Edited by Claudia Hine, Managing Editor
Norkol Converting Corp. is one of the nation's leading, independently owned converters and distributors of commercial printing papers. Founded in 1968, the company utilizes traditional slitter/rewinder equipment to unwind, slit, and then rewind paper to new dimensions. Although conventional slitter/rewinders typically produce new widths of paper with clean cuts, the company was looking for a faster option.
“Rewinders have been used for years in the paper converting industry, and although they do the job, we are constantly researching and adopting the newest technologies to help us remain competitive,” says Mike Maloy, president. The company turned to system integrator Mapleroc Industries and its automation partners, ABB Robotics and ATI Industrial Automation, to implement a new cutting and finishing system to speed up the process.
“Our original rewinders take between 30 and 40 minutes to process one roll,” says Maloy, “so we were very excited when we were introduced to new technology that processes four to six rolls per hour without the need to unwind and rewind.”
Slit Without Winding
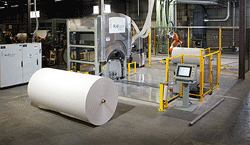
Mapleroc's RollRazor cutting technology features a highly engineered cutting blade capable of cutting as much as 300% more paper in one hour than traditional slitter/rewinders. RollRazor can cut parent rolls of paper in their rolled state in one pass, cutting them to press-ready roll sizes in three minutes, without the need to unwind and rewind the paper. The system is capable of handling all grades of paper, including tissue, napkin, cigarette, bible, coated, uncoated, paperboard, and kraft.
The RollRazor's circular blade reportedly generates virtually no heat, cutting seamlessly in one pass through the roll and maintaining the paper quality of the mill-wound roll. This avoids possible errors inherent in the unwinding and rewinding process, such as wrinkling and tension problems, and ensures consistent mill-wound rolls with all the “original” manufactured specs still built into the press-ready rolls.
Roll Finishing System
Traditional slitting/rewinding equipment makes a clean cut, and the new rolls do not require any additional finishing. The RollRazor blade cuts through the entire roll with a circular saw blade. Because not all rolls are wound the same, not all cuts come out the same.
In an effort to remove the “witness lines” that are left over from the cutting process and produce a consistent-looking roll, these edges then require “sanding” to meet the customer's requirements. To complete the robotic cutting application, the partners developed a roll finishing solution to sand and smooth the edges automatically.
The system utilizes ABB's IRB 6620 class robot equipped with a force-controlled machining package. The robot is equipped with an end-of-arm roll finishing tool and an integrated dust collection system. As the robot sands the rolls, the dust collection system removes the excess paper using a vacuum.
The IRB 6620 is a flexible and agile six-axis robot with a large working envelope. It features a compact design, has a reach of 2.2 m, and can handle payloads up to 150 kg.
With the cut roll moved into place, the robot, equipped with the sanding head, smooths the edges utilizing ATI Force/Torque Sensor technology to provide force feedback. This enables the robot to have a “sense of touch” just as a human would. This also allows the robot to make quick adjustments in real-time to maintain a constant contact force — all the while mantaining an average finishing temperature of 85 deg. Together, the robot and sensor make this finishing task possible.
The system uses ABB's force control package featuring the Force/Torque Sensors integrated onto the robot wrist where the signals from the Force/Torque Sensor are interpreted directly into the motion control of the robot. The package includes ABB's RobotWare Force Control Machining software with a user-friendly machining graphical user interface (GUI). The hardware includes an axis computer, data acquisition board for the sensor, cabling between the sensor and controller, and ATI's Force/Torque Sensor.
Sensor Technology
The key to smoothly sanding the paper rolls to meet the high standards Norkol's customers require is the system's sensor technology. The Multi-Axis Force/Torque Sensors measure all six components of force and torque. It consists of a transducer, shielded high-flex cable, and an interface card specially designed to work in the ABB robot.
When you apply a load to the transducer, it causes microscopic strains to develop on its internal beams. Silicon strain gauges placed on these beams react to the strains, and electronics measure this reaction. Software analyzes the measurements and is able to report and transmit the information about the amount of load that is being applied.
The transducer bends microscopically; it measures that bending; and the software determines and transmits that information to the robot. Simply put, the sensors are giving the robot force feedback, such as the unit is pushing too hard or moving to the left or right.
Benefits & Results
Utilizing the new RollRazor cutting technology has significantly sped up Norkol's converting process and reduced its costs. The company estimates it now can produce one press-ready roll in six minutes when it originally would take approximately 30 minutes to process. This translates to increased production, which in turn, lowers its cost per ton and cost of labor. The new equipment increases plant flexibility, maintains original mill roll quality, guarantees original sheet orientation and web tension, and also can convert wet or damaged rolls.
The Robotic Roll Finishing System with its force/torque sensing capability eliminates safety risks for employees and offers converters a quick and efficient method of finishing the roll to the standards required by the customer. The system reportedly allows the robots to address all roll sizes and unfinished surfaces automatically, eliminating the need for manual setup. With this new system, everything is embedded in the robot control, thereby eliminating the need for an expensive programmable logic controller (PLC), which typically would be used to regulate pressure and prevent the paper from burning or melting.
“We have been very pleased with the new cutting and finishing system, as it is faster and eliminates problems for most applications. We are currently evaluating and considering replacing additional rewinders with this more efficient system,” says Maloy.
Supplier Info
-
Mapleroc Industries | www.mapleroc.com
-
ABB Robotics | www.abb.com
-
ATI Industrial Automation | www.ati-ia.com
Converter Info
- Norkol Converting Corp. | 11650 W. Grand Ave., Northlake, IL 60164 | 708-531-1000 | www.norkol.com