Technical Report: Thin Coating Challenges
- Published: February 01, 2010, By By Edward D. Cohen, Edward D. Cohen Consulting Inc.
A major trend in the development of new web coated products is the requirement to coat thin, functional coatings on a thin substrate. The advantages of these coatings are reduced material cost in the product and the waste stream because of less material. Also, the raw materials for these products may be expensive, and thinner coatings reduce the amount used, thereby lowering costs.
The thinner layers can give performance advantages. More functionality can be placed in a final product, such as a battery, with a thinner film than with thick film, thereby giving better overall performance. Longer rolls can be wound without increasing roll weight.
New thin products are being developed in a variety of applications:
- Electronic | photo masks, thermal adhesive layers, antistatic layers, hard coats, OLED (organic light-emitting diode) displays
- Graphic arts | inkjet receiver layers
- Medical | transdermal patches, diagnostic strips
- Batteries | catalyst layer electrodes, separator membrane films
- Optical | adhesives and tints for window films
- Industrial | release films, synthetic paper coatings, dye surface coating
This article will discuss the technical challenges that must be overcome to successfully manufacture thin film products. It will focus on products solution-coated in a web coating process and the substrate used. The metal deposition process will not be discussed as it is a different technology and deposits different materials than in the solution process.
Definition of Thick & Thin
While the terms thick and thin are widely used, they are basically subjective terms that are influenced by the perceptions of the observer. It is possible for one technical professional to describe a sample as a “thin film” and another to call it a “thick film.” Therefore, the first challenge is an objective quantitative description of thick and thin, so the process requirements can be adequately defined and upgraded. Quantitative terms are needed to define process capability and limitations.
To obtain these definitions, several technical people were surveyed to get their understanding of the terms. The results of the survey showed a wide variety of units are used to describe thickness. Therefore, all the units reported were recalculated to mils [0.001 of an inch or 25.4 micrometers (microns)] for easy comparison, and an average was calculated for coatings and substrates. The results are summarized in Table I.
Challenges To Resolve
There are several technical challenges that must be solved to efficiently coat thin products on a web coating line. The overall coating process, coating methods and operating variables, solution handling, drying, and web transport must be optimized for a thin coating to produce defect-free film at low cost.
The majority of coating lines are designed to accommodate specific product and process needs. Often, they cannot operate effectively outside of these design limits. Therefore, coater components must be upgraded to meet thin product needs. Reformulation of coating solution may be needed also.
Next Page: Coating Method Capability
Coating Method Capability
The first challenge is to ensure the coating applicator can apply the thin coating solution with no defects. Each coating method has a coatability window, in which a defect-free product can be coated, and a range of variables, in which it functions effectively. Figure 1 is a typical window for the slot die coater. It shows the defect-free operating window and defects that occur when outside of this window.
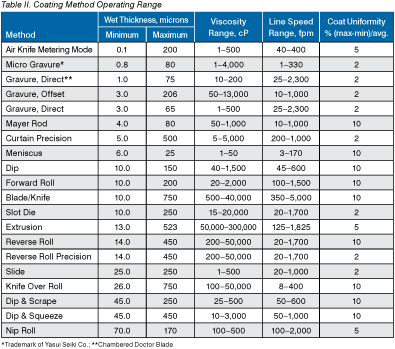
There are two factors that must be optimized to coat thin films. The first is to select the method that can coat the needed wet film thickness. Table II shows the wide range of minimum wet thicknesses for widely used coating methods as well as other operating variables. If a wet thickness of 1 micron is needed, a knife-over-roll coater with a minimum of 26 microns will not work. One of the methods at the top of the table, such as Micro Gravure, must be used. The coater selected should operate in the center of the coatability window.
The second factor is to optimize the coating solution to obtain a wet coating thickness that can be reproduced consistently. The wet thickness can be adjusted by diluting the coating solution to give an increased wet coating thickness. This will permit more methods to be considered. However, as the coating solution is diluted, the viscosity will decrease. Since there is also a viscosity range limitation for all coating methods, the viscosity reduction can lead to coating defects because the coater is operating outside of the defect-free operating range. Rheology modifiers may be needed to adjust viscosity to stay in defect-free operating range. Other coating additives also may need to be adjusted for optimum results.
Next Page: Solution Handling
Diluting the coatings increases the drying load, and if there is drying limitation, the line speed must be decreased in order to dry the coating. The speed reduction will reduce productivity and increase costs. It can result in decreased coating stability and an increase in defects, as shown in Figure 1. It also indicates the coating speed is a significant variable with higher line speeds leading to a wider region of defect-free coating.
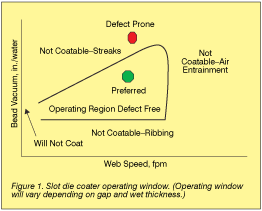
Conversely, as the line speed is reduced, the defect-free region decreases, and at some point, the solution will not coat. Therefore, as line speed is decreased from dilution, poor coating quality will be obtained.
Solution Handling
The thinner, lower viscosity coating solutions also require modifications of the solution handling system that supplies the coating applicator. The filtration system needs to be adjusted for the thinner coatings. The reason is that the particle size of the filter may need to be lowered so that particles thicker than the wet coating are not present. A 10 micron particle in a 2 micron wet coating will cause a defect. A lower-rated filter will be needed.
Low viscosity solutions are prone to bubbles, so they need to be removed, as bubbles in coating can cause spot and streak defects. The layout of the feed and return lines should be adjusted so there is no air drawn into the system. A debubbling system may be required. The performance of supply pumps must be calibrated to ensure they have the needed delivery rate and uniformity for the lower volume solutions. The solution delivery rate may be too high for the reduced volume of the thinner coatings. New pumps may be needed to meet solution delivery requirements.
Measurement Capability
For effective quality control and a reproducible product, the coated thickness and quality level must be measured and controlled. As the coating gets thinner, some measurement parameters, such as weight measurement for coating weight or basic micrometers for thickness, may not be effective, because they do not have the accuracy needed for thin coatings. New on-line measurement techniques, such as beta, gamma, X-ray transmission, infrared (IR) gauge, beta backscatter, and X-ray fluorescence, have improved sensitivity to measure thinner coatings. Also, on-line measurement will give increased yields, reproducibility, and lower costs.
Next Page: Drying Issues
Drying Issues
The basic challenge in the drying process is to dry the wet coating without introducing defects and to track a thin substrate (under 1 mil) through the coater without contacting the drying nozzles. The low-viscosity coatings are fragile because of the reduced viscosity and can be damaged easily in the dryer by high air velocity, 2,000-6,000 fpm, impinging on the coating. This velocity will move the coating, create defects, and can function as an air knife removing all of the coating.
The basic principle to avoid these defects is to do the initial drying, ~10%-15%, under mild conditions, and then use standard high rate drying for the balance of the drying. There are several possible methods to accomplish this. Use a zoned dryer with low slot velocity in the initial zone that will not disturb the coating. As the coating dries and becomes more concentrated in the first zone, it will become rigid; higher slot velocities can be used in subsequent zones.
In a floater dryer, a rear-side-only nozzle can be used to dry the film without air movement on the wet side. A first zone dryer using parallel flow air also is effective.
For water-borne coatings, an IR dryer also can be installed before the air impingement dryer. This will rapidly remove moisture without damaging the coating so the full capacity of the standard dryer can be used. Another advantage to the IR dryers is that they will add drying capacity and compensate for the increased drying load from dilution.
In a floater dryer, the web stability is a function of the base thickness, tension, and air velocity. The result is an operating window for web stability (Figure 2). The thinner substrate will require lower tension and adjustments of the slot velocity to stay in the operating window. Too high a slot velocity can result in the thin substrate being pushed into touching nozzles.
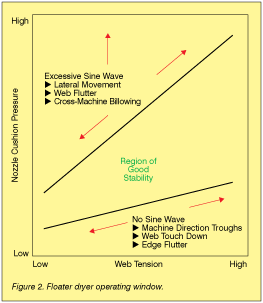
There are also other defects that can occur. For example, in a floater dryer, the substrate's baggy edges can lead to edge flutter. This flutter will result in contact between the wet coating and the nozzle, which will lead to defects and dryer cleaning issues.
This problem can be solved by using an improved planarity substrate and proper selection of nozzles. Separate tension control for the dryer will permit optimization of tension levels in the dryer to stabilize the web without affecting the rest of the coater.
The transition area between the coating applicator often is exposed to ambient room air. This exposure can damage the fragile coating. Isolating this area may be needed.
Substrate Requirements
The thin substrate will require improved thickness uniformity and low level of planarity defects, such as edge buckle, in order to permit good tracking and roll winding. The variations in the thickness profiles must be less than the thickness of the wet coating weight in order to ensure a coating on the surface of the substrate. Otherwise the solution will fill the valleys, and there will not be a uniform functional coating. Also, the profile variation can influence the gap in the coater and will affect quality.
Thinner substrates will require lower tension levels than thick substrates to avoid distortion and ensure good web handling and winding characteristics. The web handling systems often are designed for thick coatings and may not have the necessary tension control. Systems need to be evaluated, and hardware upgraded where needed.
The key to producing thinner coatings successfully is to recognize that a coating line used for thick products will require modifications to eliminate the technical challenges. These modifications are technically feasible; however, they must be recognized and corrected to ensure a successful thin film coating process.
Edward D. Cohen is a technical consultant for the Assn. of Industrial Metallizers, Coaters & Laminators (AIMCAL). He has 40+ years of experience in research and manufacturing technology. Contact him at 480-836-9452; cohened146@aol.com.
This article, along with future articles by other authors, is provided as a cooperative effort between PFFC and AIMCAL. Authors contribute to AIMCAL's technical and education offerings, which include the association's Fall Technical Conference, Converting School, AWEB Applied Web Handling Conference, and Ask AIMCAL. Visit www.pffc-online.com/events for meeting dates and locations.
The views and opinions expressed in Technical Reports are those of the author(s), not those of the editors of PFFC. Please address comments to the author(s).